Contact and proximity lithography are the simplest methods of exposing a photoresist through a master pattern called a photomask (Figure above). Contact lithography offers high resolution (down to about the wavelength of the radiation), but practical problems such as mask damage and resulting low yield make this process unusable in most production environments. 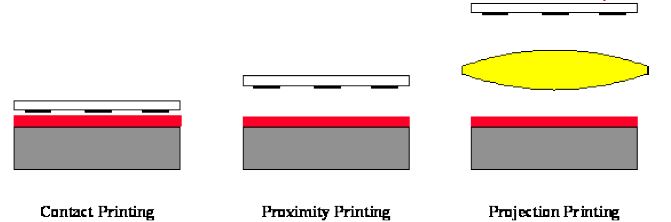
Figure: Lithographic printing in semiconductor manufacturing has evolved from contact printing (in the early 1960s) to projection printing (from the mid 1970s to today).
Proximity printing reduces mask damage by keeping the mask a set distance above the wafer (e.g., 20 ?m). Unfortunately, the resolution limit is increased to greater than 2 to 4 ?m, making proximity printing insufficient for today’s technology. By far the most common method of exposure is projection printing.
Projection lithography derives its name from the fact that an image of the mask is projected onto the wafer. Projection lithography became a viable alternative to contact/proximity printing in the mid 1970s when the advent of computer-aided lens design and improved optical materials allowed the production of lens elements of sufficient quality to meet the requirements of the semiconductor industry. In fact, these lenses have become so perfect that lens defects, called aberrations, play only a small role in determining the quality of the image. Such an optical system is said to be diffraction-limited, since it is diffraction effects and not lens aberrations which, for the most part, determine the shape of the image.